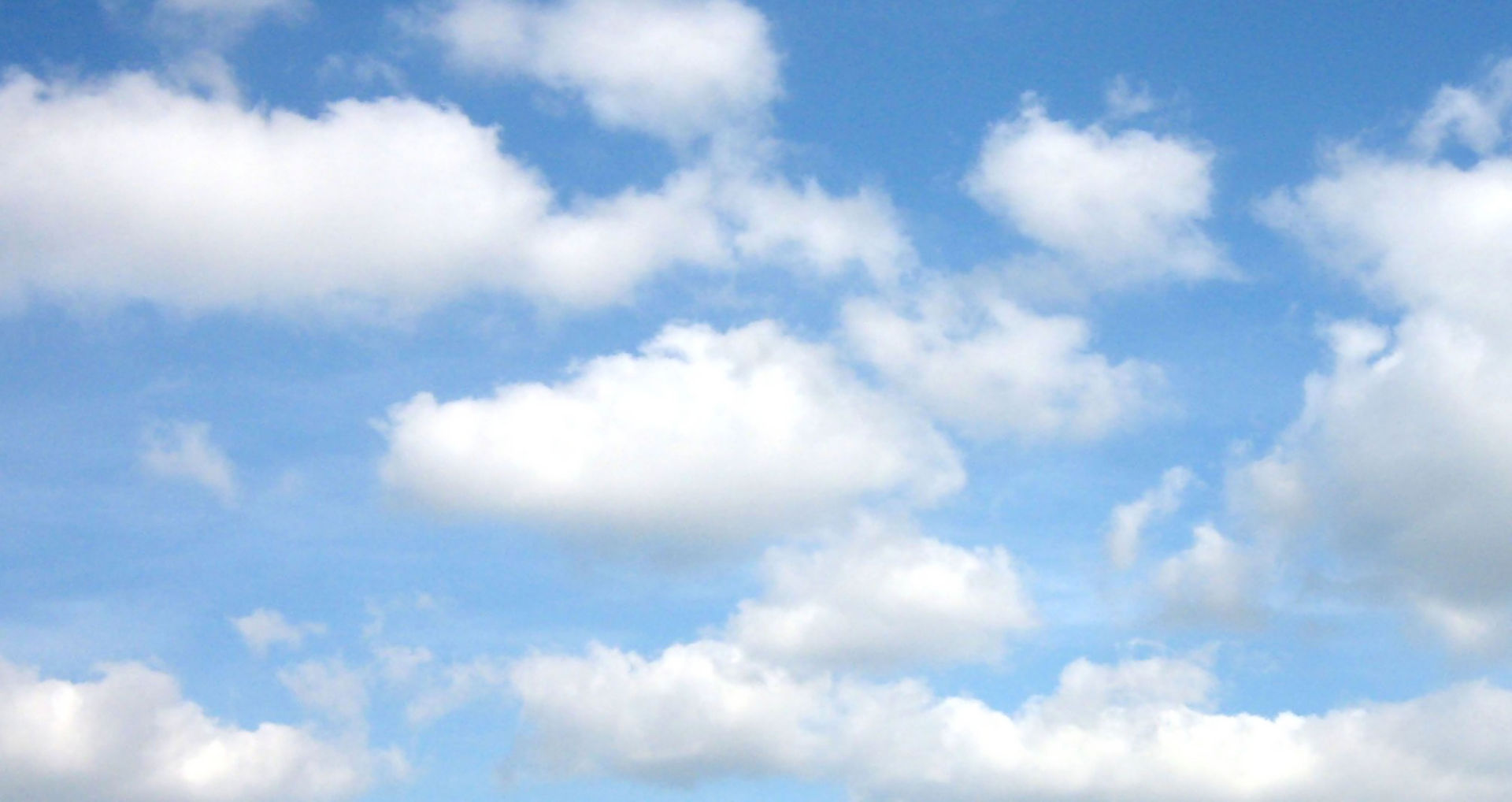
L’objectif de cette partie est d’arriver à stocker l’énergie récupérée à partir de la voile et convertie grâce aux génératrices, et d’en restituer une partie pour rembobiner les suspentes à la fin du cycle.
On peut la diviser en différentes parties :
-
partie moteur
-
partie contrôle du moteur
-
partie génératrice
-
partie mesure de puissance
Choix du moteur
Le moteur a une double fonction :
-
une fonction générateur, il doit transformer l’énergie mécanique récupérée en énergie électrique
-
une fonction moteur, il doit pouvoir rembobiner les suspentes du cerf-volant.
Pour le choix du moteur, il fallait connaître la puissance maximale ainsi que le voltage dont nous avions besoin. Nous avons décidé de travailler en 24V. Pour la puissance, il a fallu faire quelques calculs :
Lorsqu’on est dans la phase de déroulement ou lorsqu’on rembobine, la vitesse de rotation est à
peu près constante. On peut donc calculer le couple. En effet : Couple moteur = Couple résistant.
Lors d’une expérience réalisée sur une voile plus grande, d’autres étudiants ont déduit la force
maximale qui pouvait s’exercer sur le cerf-volant : 100N. Sachant qu’on déroule les suspentes à
2 m/s, la puissance est donc de 200W. Avec un cylindre de rayon 2cm, le couple est de 2 N/m.
Lors du changement de phase ou démarrage du moteur, il faut considérer la variation de rotation
soit le terme en J*(dω/dt).
Pour calculer le J, on fait une hypothèse grossière : on modélise le cerf-volant par une
demi-sphère creuse. On déduit que le couple peut atteindre 2,5 N/m. La puissance maximale est
donc de 250W.
La plupart des moteurs ont une vitesse de rotation à vide d’environ de 3000 tours/min soit
environ 314 rad/s.
Nous avons choisi un moteur à courant continu CC de 24V et de 250W.
Voilà ses caractéristiques :
Le poids du moteur est de 1.87 kg, il est équipé d'origine d'un pignon de 11 dents au pas 1/4" (6.35mm), ayant une largeur de 3mm.
Le moteur se fixe via un socle de fer percé de 4 trous filtés M6.
Le couple disponible en sortie d'arbre moteur est proche de 0.9 N.m, pour une puissance proche de 253W.
Un réducteur sera nécessaire car le couple du moteur est trop faible par rapport au couple exercé par le cerf-volant, calculé précédemment.
En effet, pour déterminer le rapport de réduction, on calcule le couple grâce à la puissance et à la rotation soit C = P/ω = 350 / 314 = 0,80 N.m
Comme le couple maximal est de 2,5 le rapport est donc de 2,5/0,8 = 3.
Contrôle du moteur
Maintenant que le moteur a été déterminé, il faut le contrôler. La carte de puissance, qui est une sorte de hacheur, permet de relier la batterie au moteur. Grâce aux conseils des professeurs et à l’intensité nominale du moteur, nous avons choisi la carte de puissance MD03 24V 24A. Nous l’avons choisie à partir de deux éléments : le voltage de la batterie (24V) et le courant nominal du moteur. Le courant élevé que peut supporter la carte permet de gérer toutes les hausses de courant dues notamment aux réducteurs.
Cette carte de puissance a le grand avantage de posséder un microcontrôleur qui permet de mesurer le courant. Nous pouvons donc nous passer de multimètre pour les mesures d’intensité et de puissance. Plus tard, ces données pourront être affichées sur un écran de contrôle. Nous avons donc relié cette carte de puissance à un microcontrôleur Arduino Uno, pour analyser et produire des signaux électriques.
Le code Arduino permet plusieurs choses :
-
régler la vitesse : on la règle avec un nombre entre 0 et 255 sur le code Arduino. Ce nombre correspond à une vitesse de rotation du moteur. Nous avons donc tracé une courbe de correspondance des valeurs pour afin de commander la vitesse facilement.
On remarque qu’en dessous d’un certaine valeur (environ 10) le moteur ne tourne pas.
-
calculer l’intensité : on peut la lire avec la carte de puissance. Pour cela, il faut retirer l’intensité nécessaire pour alimenter la carte et multiplier par un coefficient (0,15). La datasheet nous donnait un certain coefficient qui n’était pas exact. Nous l’avons changée grâce à un ampèremètre permettant de mesurer le courant de deux manières différentes.
-
calculer la puissance en multipliant l’intensité par la tension, ici 24V.
-
changer le sens de rotation du moteur (backward ou forward)
Nous avons tracé une seconde courbe qui permet de savoir quelle est la tension aux bornes du moteur en fonction de la rotation du moteur. Ces deux grandeurs sont dépendantes linéairement. Cet essai a été réalisé à vide.
Choix des batteries
Nous avons choisi des batteries 12V au lithium par un souci de poids. En effet elles pèsent moins lourd que des batteries en plomb bien qu’elles soient un peu plus chères. Elles seront branchées en séries pour être équivalentes à une batterie de 24 V.
Protection
Nous avons rajouté deux fusibles dans le montage pour protéger les composants, notamment la carte de puissance.
Ils sont placés entre la batterie et la carte de puissance et entre la carte de puissance et le moteur. Les fusibles utilisés sont des fusibles tubulaires 25A.
Pour les insérer dans le montage, un porte-fusible était indispensable.
La protection contre l’élévation de température n’est pas utile car l’échauffement est négligeable.
Electricité




